Many domestic automobile manufacturing and assembly enterprises are currently facing difficulties due to the shortage of imported parts, especially from China, caused by the effects of the COVID-19, according to the Ministry of Industry and Trade (MoIT).
Enterprises producing and assembling commercial vehicles including trucks and buses in the country, which currently mainly import components from China, are most affected.
Truong Thanh Hoai, director of the MoIT’s Industry and Trade Department, analysed that it is difficult for high-quality raw materials and components for cars to be sourced in the short term as the global production chain is organised in a complex way and require parts to exactly meet the technical requirements.
Additionally, the import of spare parts and input materials was also affected by the epidemic’s outbreak in other countries, such as South Korea, Japan, and India.
Industry insiders said that finding alternative sources right away will be very complex, and that there is currently no escape out of the misery. It is expected that production activities would decrease significantly by mid-March if the situation is not improved.
“Enterprises need to seek other supply sources rather than from China. However, this could be a simple job for other industries, but not for auto manufacturing,” said Hoai. “The production chain will be interrupted if they lack just one small component. The reliance among countries in the production chain is very heavy.”
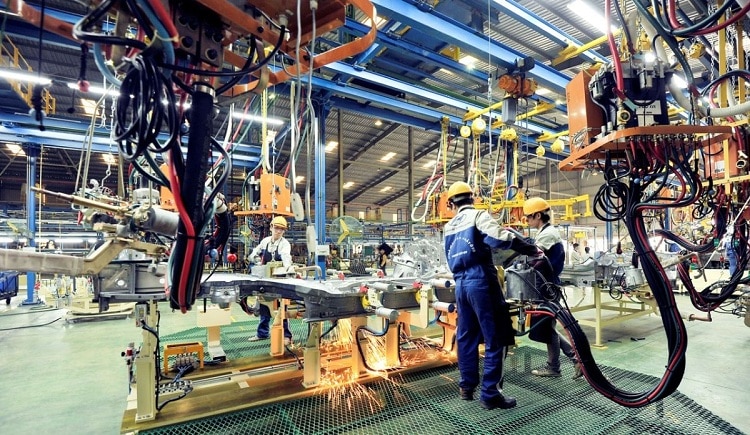
A domestic automobile manufacturing and assembling enterprise in the northern province of Hung Yen said that the automobile market has witnessed a gloomy picture contributed by weak demand and shortages in parts and components due to the outbreak.
He added that his company is faced with the suspended production due to a lack of components, leading to a delay in implementing the firm’s plan to launch a new model.
Previously the firm could produce and sell about 1,000 trucks a month. However, sales have been chopped by half thus far.
In 2019, Vietnam imported nearly $4 billion of auto parts, of which imports from China reached $700 million (17.5 per cent), from South Korea $1.14 billion (28.55 per cent), and from Japan $720 million (18 per cent).
The local supporting industry remains limited, with almost all components for assembly being imported. In general, although parts like tubes, tires, seats, mirrors, and batteries can be produced locally, they often do not meet the technical standards required for the automobile industry.
Up to 90 per cent of the main raw materials for the production of such components, like aluminium, plastic resin, and high-tech rubber are imported, creating higher costs in the transport, packaging, and taxes.
Currently, some foreign automobile makers like Toyota, Honda, and Ford import components from Japan and Southeast Asian countries. Meanwhile, local automobile manufacturers and assembly enterprises mainly import components from South Korea and India.
According to the foreign newswires, several component suppliers in China’s Wuhan City and Hubei provinces have alerted their customers that they are unable to maintain the supplies. Similar problems have also emerged in South Korea and will likely spread to other countries and regions as well.
The coronavirus epidemic could have a domino effect on the global automobile industry. For instance, Hyundai will suspend production in South Korea due to the outbreak that disrupted the supply of parts, following Nissan suspending auto production in Japan’s Kyushu plant.
The previous lack of coherent government policies, combined with weak incentives for completely knocked down assemblers and poor supplier presence, has resulted in a local manufacturing environment that is less attractive for automakers than in other ASEAN countries, according to the Vietnam Business Forum. VIR
Source: vietnamnet.vn